Brake discs are the large metal disks in front of car wheels that slow and stop the vehicle by friction. The basic function of brakes is simple: calipers push one or more pads onto the disc, creating friction and slowing the rotation of the axle the wheel is attached to. The details vary widely, though: the type of caliper, pad material and size, disc design and shape, even how the disc is fixed to the hub.
Despite the differences, all car brakes work on the same basic principle: kinetic energy is converted into thermal energy. This energy is transferred to the brake disc and pad via friction, with the disc and pads reaching high temperatures during braking. To prevent these high temperatures and excessive wear, the brake disc must be made from a strong material that can withstand the high levels of friction generated and the temperature rise caused by the thermal stress.
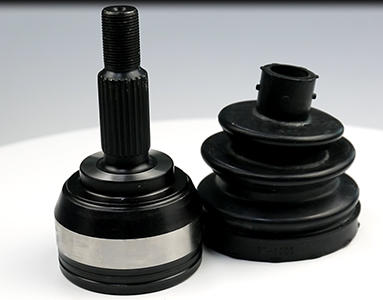
One way to achieve this is by using a material with high mechanical strength and low thermal conductivity, such as aluminium-magnesium-cobalt (ALMMC). Aiming to improve performance, we have carried out structural and thermal analyses on various types of brake discs made from AL-MMC. This has allowed us to predict the temperatures, distribution and stresses that will be generated during braking. The results showed that model ALMMC had the lowest predicted surface temperatures, indicating that it has good tribological properties.
This is important because the disc can only be machined a limited number of times before it is damaged beyond repair. Abrasion, which can lead to scoring, is a common problem and can reduce the thickness of the disc, meaning it must be replaced. In some states, such as Pennsylvania, it is illegal to drive a car with a brake disc that has scored beyond the minimum rated safe thickness.
The analysis also confirmed that the axial stresses developed by the disc were negligible, although concentrated stress was found around the holes in the rotor and in parts of the ventilation blades. Such high stress can cause the rotor to crack and the disc to fail.
The analysis also showed that the maximum out-of-plane bending displacement of the disc was found near the bolt hole, where the maximum alternating tensile and compressive stresses were found. It is important to minimise this value to increase the lifespan of the rotor and avoid any damage to the bolt. This can be achieved by carrying out an optimal design for the braking system using the results from this study. Optimal design is based on the orthogonal arrangement method with factors that have the largest effect on the objective functions being used to find the best design. By doing this, it is possible to produce a disc that has better thermal stability and cooling performance than the existing ones. This will lead to reduced brake disc temperatures and a significant reduction in disc coning. This is a crucial factor in improving the safety and reliability of cars.