Brake discs are a common feature on modern cars and are responsible for the vast majority of the stopping power in the vehicle. They work on the simple principle that when a caliper pushes brake pads against the disc, friction is generated which slows the rotation of the axle the wheels are attached to. Despite this basic concept, there are many different variations in the design of brake systems from one car manufacturer to another and even among aftermarket parts. Pad material, rotor design, and caliper style all have a significant impact on how well a disc brake performs.
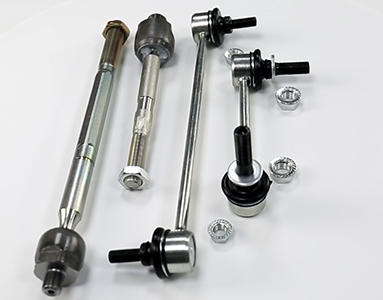
In a hydraulically actuated disc brake, slave pistons in the caliper are forced against the pads by hydraulic pressure, producing a normal force at each pad/disc interface. This eliminates the need for springs or other retraction mechanisms, and results in the brake pedal force being more evenly distributed over the entire braking area of the wheel. The hydraulic seals also provide a small amount of piston 'rollback' which can help to compensate for the fact that a brake disc generates heat over the braking region.
When a disc brake is first used, the rotor and pads both experience a rapid increase in temperature. This is because the braking action draws heat from the pads into the disc, and as the brakes are applied and released, this temperature rise and fall is amplified by the varying force of the caliper against the rotor. Consequently, the'start-of-stop' temperature is commonly taken as the reference for performance testing of resin-bonded brake discs.
The goal of this study was to investigate the structural and thermal behavior of a ventilated disc through a Finite Element Analysis (FEA). The ventilated disc is constructed with two solid discs that have ventilation blades between them, which allows for cooling channels in the disc. The structural analysis was conducted to identify the stress distribution on the surface of the rotor, while the thermal analysis was used to determine the temperature profile in the rotor.